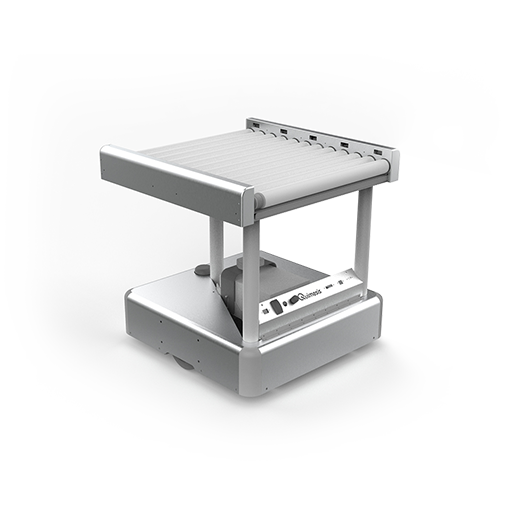
AGV
Quimesis has developed an autonomous robot capable of sorting parcels with greater efficiency than using conventional belt conveyors. 24 hours a day, 150 robots moving at 3m/s to sort your parcels.

100% autonomous postal sorting robot
Who's there?
Quimesis, in association with ISITEC (France), has specialised in the development of a new robotic platform. Our vision is to bring disruptive change across key sectors of the economy. And this by working with the leaders of these sectors in order to access the 4th industrial revolution.
Who's it for?
In this philosophy, one of the sectors addressed is the Supply Chain. The focus is on one part of the chain, namely the sorting centres.
Currently, the sorting of parcels from aircraft to trucks is done via automated multi-level roller conveyor systems. These infrastructures are very expensive and lack flexibility. During periods of high intensity, it is not possible to temporarily expand the facility. And when activity is low, such machinery is not necessary. Moreover, there is also the risk of complete blockage of the chain if a package is not recognized.
To overcome these drawbacks, Isitec and Quimesis have created a "sorting robot". The aim is to have mobile robots that can locate themselves indoors and orient themselves according to the parcel they are carrying and the position of other robots present. The group of robots works like a swarm of bees. These robots move at 3 meters per second, and can carry up to 35 kg. For information, a sorting center needing to sort 10,000 parcels per hour would require 150 robots.
Development
When the project began, Isitec went in search of a technological partner who could be responsible for the design of such a robot.
Quimesis came into play and a partnership was sealed.
Thanks to the artificial intelligence embedded in each robot, it will be able to orient itself in its environment, recognize and bring packages to the right place and avoid other robots.
This project includes a lot of aspects, including power mechanics, i.e. the motors, the battery supply, the realization of the wiring, the choice of the materials that would compose the robot's framework, the implementation of the safety systems, among others. As for the electronics, it was necessary to install a spatial recognition and obstacle detection system using Lidars, interfacing a whole series of sensors such as those that will detect the presence of a package and those that determine its weight.
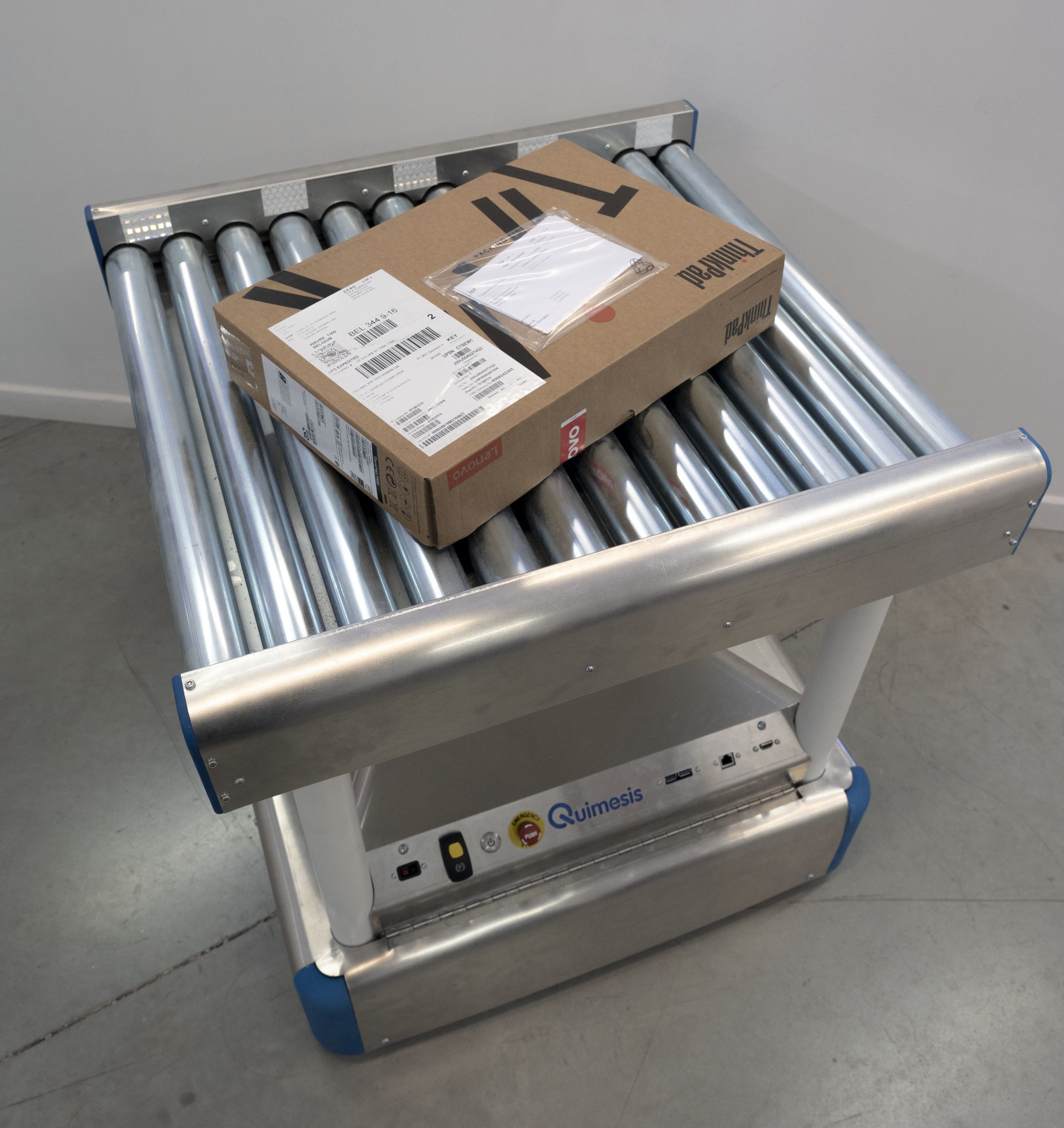
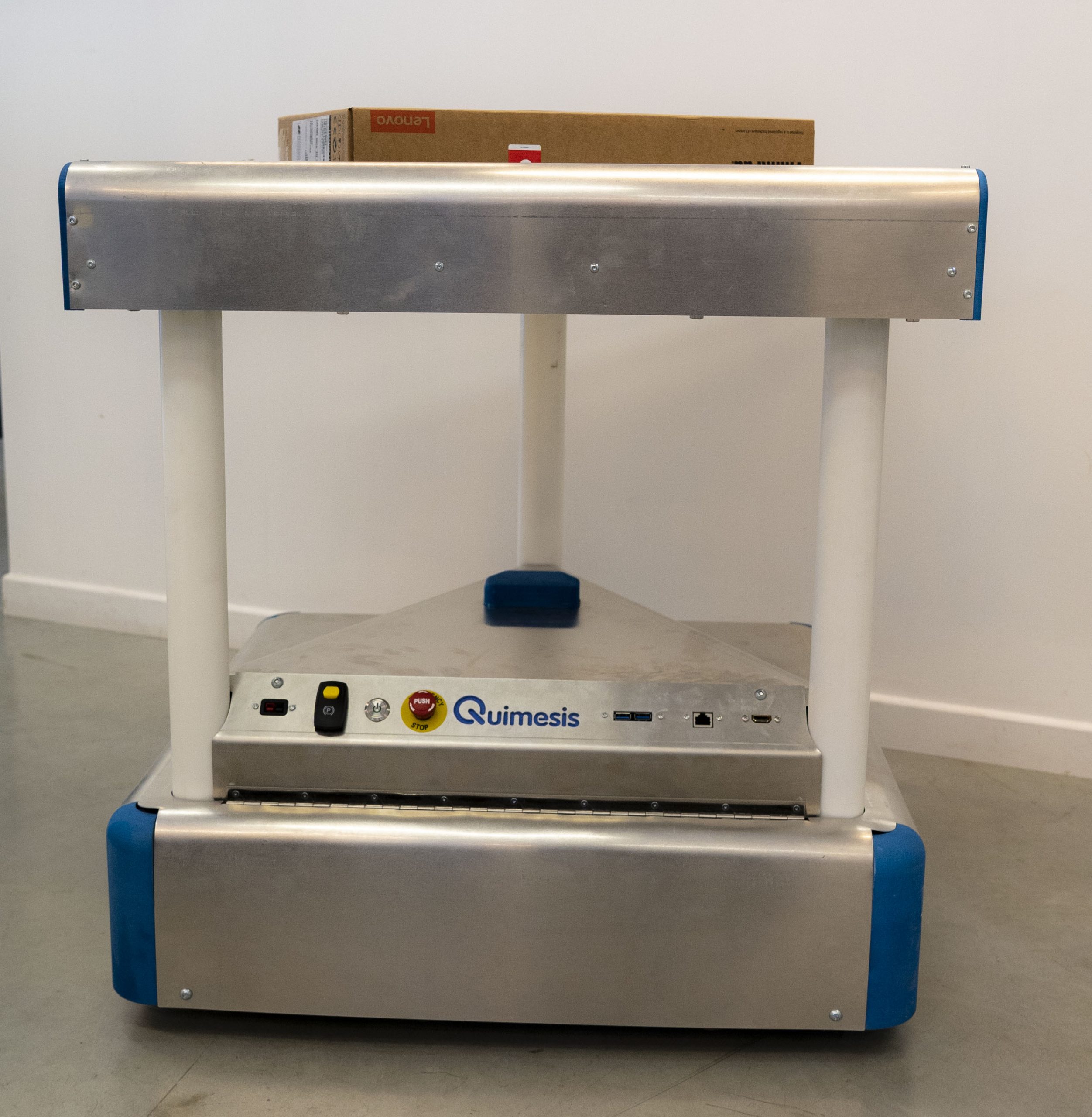
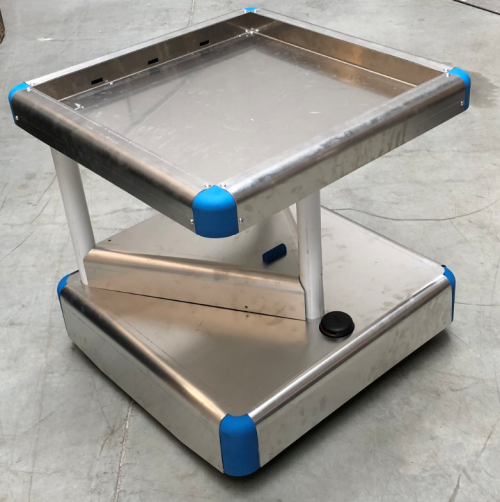
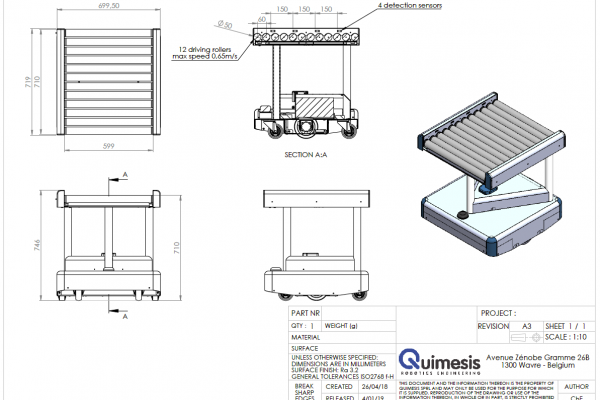